What Is DOM Tubing and How Is It Used? Explained and Uses
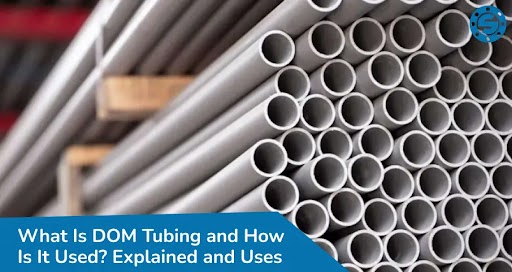
Steel tubing is a widely used metal product with countless applications. While it may appear straightforward, the variety of steel tubing options is extensive. One particular type of tubing, known as DOM (Drawn Over Mandrel) tube, has unique qualities that set it apart. In this article, we’ll explore how DOM tubing is made and its common uses, helping you decide if it’s the right choice for your project.
What Does DOM Stand For?
DOM stands for Drawn Over Mandrel, which is a manufacturing process used to produce high-quality steel tubes, typically from 1020/1026 electric resistance steel. The term “DOM tubing” refers to the method used to finish the tube, rather than the material itself. This process enhances the strength and precision of the steel tube, making it ideal for demanding applications.
How is DOM Tubing Made? (Part A)
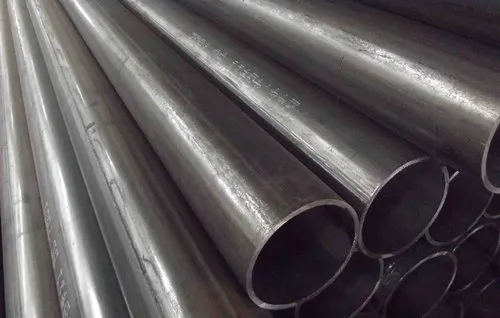
DOM tubing is made using a process similar to standard electric resistance welded (ERW) tubes, but with an additional step for improved quality. It begins with coils of steel being slit to the required size. The edges are then welded together using an electric resistance welder, forming the basic tube shape. After testing to ensure it meets industry standards, the tube is cut to the desired size. While this is where regular ERW tubing ends, DOM tubing continues with an extra process to enhance its strength and precision.
How is DOM Tubing Made? (Part B)
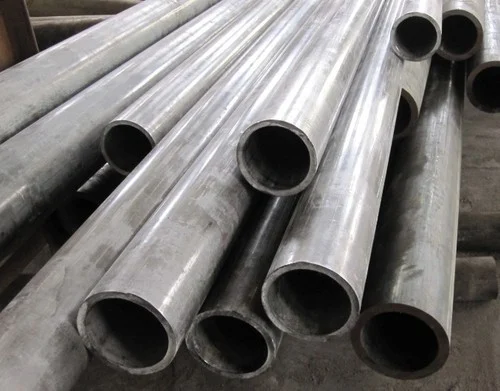
After the initial ERW process, DOM tubing goes through an additional step. The weld flash is removed, and the tube is cold drawn over a mandrel—hence the name “Drawn Over Mandrel.” This cold drawing process refines the metal’s structure, improving its grain size and alignment, resulting in a stronger, longer tube. The process also ensures precise control over both the inner and outer diameters, creating a tube with uniform thickness and a high strength-to-weight ratio.
While DOM tubing appears seamless, there is actually a seam on the interior. However, the welding process ensures that this seam is nearly invisible. This makes DOM tubing stronger, more precise, and more durable than standard tubing, making it ideal for a wide range of mechanical applications. According to the Steel Tube Institute, DOM tubing is not only cost-effective but also offers closer tolerances, better machinability, and more size options.
ERW Briefly Explained
Electric Resistance Welding (ERW) uses pressure and electrical currents to create a weld. In this process, high-frequency electrical currents generate heat, which forges the weld between the edges of the steel. This method, particularly Cold-Pressed Electric Resistance Welding (CERW), is the initial step in making DOM tubing.
What Are Common Uses & Applications of DOM Tubing?
DOM tubing is known for its reliability, affordability, and smooth surface, making it suitable for a wide range of applications. It’s commonly used in race car frames, roll cages, hydraulic cylinders, and agricultural equipment due to its high strength-to-weight ratio.
In the automotive industry, DOM tubing is used for various components such as axles, steering columns, shift levers, airbag inflators, power seat mechanisms, engine mounts, fuel rails, and injection components. It also plays a role in stationary vehicle parts like headrests and seat frames.
Beyond vehicles, DOM tubing is a top choice for rollover cages and is crucial in hydraulic presses, torque wrenches, and snowmobiles. In construction, it is used for augers, chassis, crane boom lacings, and as integral parts of infrastructure like columns and railings.
Interestingly, DOM tubing also finds applications in the energy sector, including components for solar brackets, wind turbines, and various parts in coal, nuclear, and electric plants. Its versatility allows it to replace many types of steel tubes, offering flexibility in both static and dynamic applications.
Is DOM Tubing Right For You?
If you need a steel tube with consistent wall thickness, strong grain structure, high yield and tensile strength, and a smooth surface, DOM tubing could be the ideal choice. The drawn-over-mandrel process enhances the tube’s strength and durability, providing superior weld quality.
DOM tubing stands out for its ability to handle demanding applications and its versatility across various uses. If your project aligns with the applications and benefits of DOM tubing, it’s likely a reliable and effective solution for your needs.
Conclusion
DOM tubing offers exceptional strength, uniformity, and durability, making it a top choice for demanding applications across various industries. Its smooth surface, high tensile strength, and versatile uses in automotive parts, construction, and energy sectors highlight its reliability. Whether you need precise mechanical components or robust structural elements, DOM tubing stands out as a dependable solution for your project needs.
FAQs
DOM tubing is used in high-pressure and high-load applications due to its superior strength and uniformity. It’s commonly found in automotive, oil and gas, and aerospace industries, and is often used to create critical machine parts.
DOM tubing is highly accurate with tight dimensional tolerances, uniform wall thickness, and concentricity. It also features consistent mechanical properties and controlled hardness, ensuring precision and reliability in various applications.
DOM tubing is typically made from 1020, 1026, or ST52.3 grades of steel. It is cold drawn and has enhanced mechanical properties due to the removal of flash and precise sizing.