Alloy Steel Pipe VS Carbon Steel Pipe
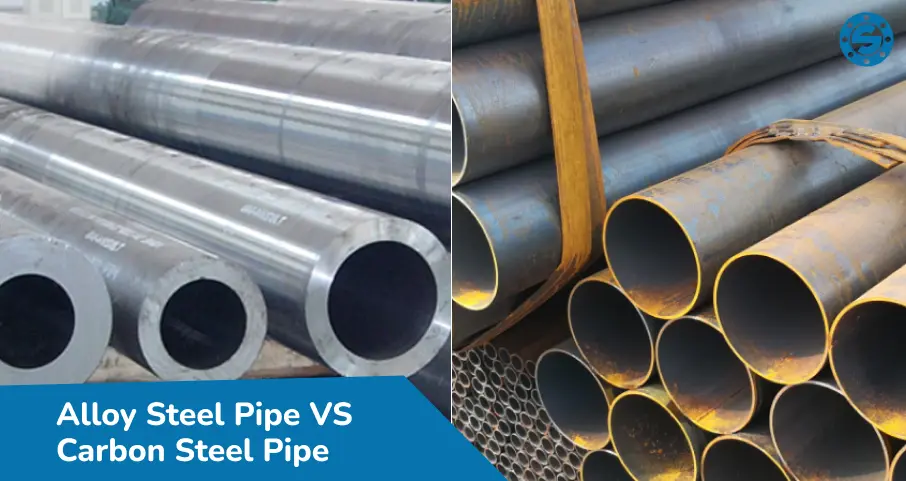
Both alloy steel and carbon steel offer valuable properties for various applications. Carbon steel, an alloy of iron and up to 2% carbon, is widely used in machinery, tools, and infrastructure due to its strength and affordability. Alloy steel, which includes additional elements like manganese, chromium, and nickel, is designed for high-strength applications such as gears and axles. When selecting steel, consider factors like strength and hardness for alloy steel or weldability for carbon steel. This guide will explore the key differences between these two types of steel to help you make the best choice for your project.
What is Alloy Steel?
Alloy steel is a steel type enriched with alloying elements such as chromium, nickel, manganese, and titanium, in addition to carbon. These elements enhance the steel’s mechanical properties, including strength, hardness, wear resistance, and corrosion resistance. Alloy steel is commonly used in construction, automotive, and aerospace industries for applications requiring specific performance characteristics.
What is a carbon steel?
Carbon steel is steel where carbon is the primary alloying element. It typically has a higher carbon content compared to alloy steel. Known for its strength and durability, carbon steel is used in automotive parts, construction materials, and hand tools. It can be heat-treated to improve hardness but is more prone to rust than alloy steel. Carbon steel components are often forged, cast, or machined.
Properties of Carbon Steel vs Alloy Steel
Property | Carbon Steel Pipes | Alloy Steel Pipes |
Composition | Iron and carbon | Iron, carbon, and alloying elements |
Strength | Lower | Higher |
Corrosion Resistance | Lower | Higher |
Cost | Lower | Higher |
Applications | General-purpose applications | High-temperature and corrosive environments |
Types of Alloy Steel
- Low-Alloy Steel: Contains carbon along with elements like manganese, silicon, copper, nickel, and/or molybdenum. These steels are generally weaker and more ductile, commonly used in construction for pipes and beams.
- High-Alloy Steel: Contains more than 5% of alloying elements such as chromium, vanadium, or tungsten. Known for their exceptional strength and hardness, these steels are used in automotive construction, power generation, and chemical processing.
- Tool Steel: Contains high levels of carbon and other elements like chromium, manganese, and tungsten. It is highly durable and hard, making it ideal for manufacturing cutting and drilling tools.
Types of Carbon Steel
- Low-Carbon Steel (Mild Steel): Contains up to 0.30% carbon. It is widely used in construction and manufacturing due to its good weldability and machinability.
- Medium-Carbon Steel: Contains between 0.31% and 0.60% carbon. This type balances strength and ductility, making it suitable for automotive components and structural parts.
- High-Carbon Steel: Contains between 0.61% and 1.50% carbon. Known for its hardness and strength, it is used in manufacturing springs, blades, and high-strength wires.
- Ultra-High-Carbon Steel: Contains between 1.51% and 2% carbon. This steel is extremely hard and is used in specialized applications like knife blades and high-strength tools.
Advantages of Alloy Steel Compared to Carbon Steel
- Increased Wear Resistance: Alloy steels are more resistant to wear and tear, making them suitable for high-impact and high-friction applications.
- Enhanced Corrosion and High-Temperature Resistance: Alloy steels can withstand harsh environments, including high temperatures and corrosive conditions, better than carbon steels.
- Improved Heat-Treatment Capability: They can be heat-treated to further increase strength and hardness, enhancing durability and performance.
- Greater Strength and Toughness: Generally, alloy steels are stronger and tougher, offering better performance under stress and demanding conditions.
Disadvantages of Alloy Steel Compared to Carbon Steel
- Higher Production Costs: Alloy steels are more expensive to produce due to the additional alloying elements and complex manufacturing processes.
- Welding Challenges: They are more difficult to weld compared to carbon steels, requiring specialized techniques and equipment.
- Increased Corrosion Susceptibility: Despite improved corrosion resistance, alloy steels can still be more susceptible to certain types of corrosion compared to some carbon steels.
- Lower Hardness and Strength: In some cases, alloy steels might have lower hardness and strength compared to high-carbon steels.
- Machining Difficulty: Alloy steels are often harder to machine than carbon steels, which can increase manufacturing costs and time.
Comparisons for Alloy Steel Besides Carbon Steel
- Chrome Steel: Chrome steel is carbon steel coated with chromium, offering high corrosion resistance. It is ideal for tools, drills, and kitchen utensils.
- Copper Steel: This alloy, combining copper and steel, is used in rail tank cars and bridges. It offers enhanced strength and resistance to corrosion.
- Beryllium Steel: Known for its high strength and low weight, beryllium steel is commonly used in aerospace applications.
- Aluminum Steel: Aluminum steel, or aluminum alloys like 3003 and 3004, provides superior properties for cooking utensils, pressure vessels, and beverage cans due to its lightweight nature.
- Magnesium Steel: Alloyed with magnesium, this steel is used in the automotive industry for its low density and high strength, improving vehicle performance.
- Tungsten Steel: Tungsten steel, combining tungsten with steel, is utilized for cutting tools and wear-resistant parts due to its hardness and durability.
Conclusion
Carbon steel and alloy steel pipes each offer unique benefits suited to various applications. Carbon steel pipes are ideal for general purposes due to their cost-effectiveness and ease of use. In contrast, alloy steel pipes excel in demanding environments, providing superior strength and corrosion resistance in high-temperature conditions. Choose the material that best meets the specific needs of your project to ensure optimal performance.