Alloy Steel P91 - A Brief Guide
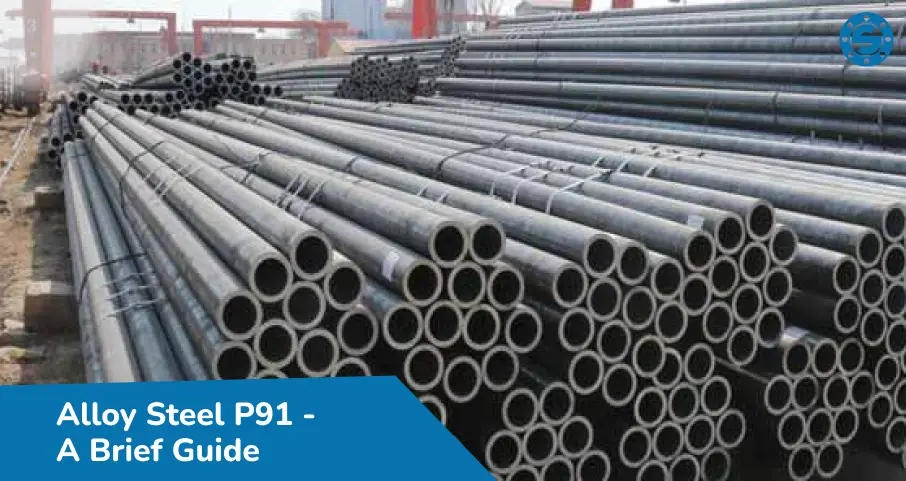
For the past few decades, the power of industry-standard materials has significantly improved with advancements in technology. T91 grade material, also known as P91, is one of the leading materials suitable for high-temperature applications. In modern boilers, steam leaving the superheater at temperatures ranging from 570°C to 600°C typically operates at pressures between 170 bar and 230 bar. The last stage in this superheater process involves carrying steam through pipes to the turbine, which must withstand these extreme conditions.
To handle these demanding environments, materials with exceptional strength and properties are required. P91 material, known for its excellent creep resistance, does not deteriorate over time, ensuring long-term reliability. Strength-Enhanced Ferritic Steel (CSEF) and advanced Chromium-Molybdenum Steels are widely used globally for their superior performance in high-temperature applications.
Using these advanced materials increases the efficiency of systems operating under extreme conditions. The superior properties of P91 and similar materials make them essential in various high-temperature applications, ensuring durability and stability even in the most challenging environments.
What is Alloy Steel P91?
Alloy Steel Pipe P91 is a high-temperature alloy steel pipe commonly used in power plants for critical applications such as heat exchangers, boilers, and petrochemical processing. This pipe is composed of an alloy containing 9% Chromium and 1% Molybdenum, which significantly enhances its creep rupture strength at elevated temperatures. This composition makes the P91 pipe ideal for use in environments where high heat and pressure are common.
One of the key advantages of Alloy Steel Pipe P91 is its excellent corrosion resistance. It can withstand harsh conditions and corrosive environments, making it a reliable choice for various industrial applications. Additionally, P91 pipe offers superior wear resistance at higher temperatures, ensuring durability and longevity in demanding settings. Its improved thermal efficiency and resistance to stress corrosion cracking further enhance its performance.
The tensile strength of P91 steel pipe is impressive, exceeding 80 ksi, with a yield strength at 0.2% offset surpassing 70 ksi. This high strength, combined with its exceptional weldability due to low carbon content, makes it suitable for critical applications where reliability is paramount. The good ductility of P91 pipe allows it to be used in industrial settings with severe temperature considerations or corrosive environments, providing a robust and dependable solution.
Why is P91 different?
P91 stands out due to its advanced composition and enhanced features, including the addition of 9% Chromium, 1% Molybdenum, and other elements like vanadium, boron, and tungsten. These additions make it significantly different from other materials. P91’s advanced chromium-molybdenum composition improves its high-temperature strength and oxidation resistance, which are critical for demanding applications.
Compared to traditional grades like P22, which contains only 0.5% Chromium, P91 offers superior performance. The higher Chromium content in P91 not only increases its strength at elevated temperatures but also enhances its resistance to oxidation. Molybdenum, on the other hand, boosts creep resistance, making the material more durable and reliable for long-term use in extreme conditions.
Additionally, elements like manganese and nickel further enhance the hardness and mechanical properties of the steel, ensuring it can withstand high stress and harsh environments. These features make P91 an excellent choice for critical applications in power plants, heat exchangers, boilers, and petrochemical industries, where high temperature and pressure conditions prevail.
Alloying elements
Advantages of P91
SA 335 P91 or SA 213 T91 is a superior ferritic alloy steel, often referred to as 9 Cr 1 Mo steel, renowned for its exceptional performance in power plant services. This grade, an advancement over its predecessor T22 or P22, can withstand temperatures up to 600 °C. Its high oxidation resistance and strength make it ideal for power plant components such as superheater coils, steam piping, and headers, allowing for thinner construction and enhanced thermal fatigue life. This contributes to higher operating temperatures and improved efficiency in power plants.
Alloy steel, including P91, contains various alloying elements such as manganese, silicon, chromium, vanadium, boron, and nickel. These elements impart specific properties, making the steel suitable for demanding applications. Alloy steels are categorized into low and high alloy steels, with high alloy steels containing more than 8% alloying elements. P91 is a high alloy steel, providing significant advantages over carbon steel and low alloy steels, particularly in applications requiring high strength and temperature resistance.
P91 alloy steel is manufactured with precision and strict adherence to industry standards, including specific heat treatment processes. These treatments ensure the steel retains its desirable properties, even after extensive use. P91 steel is particularly noted for its high yield strength and excellent corrosion resistance, making it suitable for various industrial applications, including tanker linings and structures requiring high return quality. The material’s ability to maintain its microstructure through precise heat treatment is crucial for its performance in high-stress environments.
Welding P91
Welding P91 steel is a critical process in industries worldwide, especially due to its impact on the microstructure of the material. Key factors such as post-weld heat treatment, maintaining interpass temperatures, and managing cooling rates must be carefully controlled. Thick-wall pipes often use induction heating systems for better control of both inner and outer diameters. This method helps maintain the necessary inter-pass temperatures, ensuring the steel’s structural integrity. The nickel and manganese content in P91 affects its response to heat treatment, making the composition of welding electrodes crucial for matching the parent material.
Effect of Water
Untreated P91 steel has a high affinity for hydrogen, which can lead to stress corrosion cracking when exposed to water. Preheating the steel to remove moisture is essential, and post-weld heat treatment should be performed quickly to prevent contact with water. Proper heat treatment throughout the cross-sections is vital, especially for complex geometries, to ensure the desired properties are achieved.
Applications of P91 Alloy Steel Pipes
P91 alloy steel pipes are widely used in high-temperature applications, particularly in the power industry and petrochemical facilities. These pipes, part of ASTM A335, must meet specific chemical composition, tensile properties, and hardness requirements. P91 allows for significant reductions in wall thickness, resulting in lighter hanger loads, shorter welding times, and reduced filler metal usage. The high chromium content (9% chromium and 1% molybdenum) provides enhanced creep strength and durability, making P91 superior to grades like P22, which contains only 2.5% chromium and 1% molybdenum.
Properties of P91
P91 is a chrome-moly alloy steel known for its exceptional strength and heat resistance. As a creep strength-enhanced ferritic (CSEF) material, it undergoes a specific heat treatment process—normalizing at 1050 °C, air cooling to 200 °C, and tempering at 760 °C. This treatment imparts P91 with its remarkable creep strength and durability, making it suitable for demanding industrial applications.
Summary
Alloy Steel P91 stands out for its high-temperature strength, oxidation resistance, and superior performance in power plant applications. Its precise manufacturing and heat treatment processes ensure reliable performance, making it a preferred choice for demanding industrial applications.